Reactor Types
Introduction
In Chemical industry three type Reactors used.
Chemical reactors types are essential devices used in chemical engineering to facilitate chemical reactions on an industrial scale.
They are designed to control reaction conditions such as temperature, pressure, concentration, and mixing to maximize reaction efficiency, selectivity, and yield. Here’s a brief introduction to chemical reactors types.
Reactor Types Basis On Operation
- Batch Reactor
- CSTR ( continuous stirred tank Reactor )
- PFR ( plug flow Reactor )
Batch Reactor
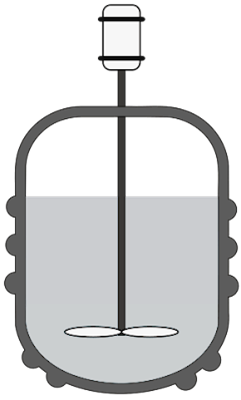
- A batch reactor is a closed vessel in which reactions happen and it is a non-continuous type of Reactor.
- The vessel contains an agitator.
- The purpose of the agitator is to mix the reactants thoroughly so that the contact makes them react together efficiently and produce products.
- The batch reactor is a non-steady, transient reactor. It means the extent of conversion within the reactor depends on time.
- Due to agitator the batch reactor is highly uniform in nature.
- To order to handle exothermic reactions the batch reactor is often equipped with cooling coils. In order to work with endothermic reactions the batch reactor has provisions for heating the reaction mixture.
- Two or more components can be added.
- After completion of reactor/ process the Reactor has to be empty out.
Where are Batch reactor Uses ?
Pharmaceutical Industry
Chemical industry
Pigment Industry
Polymer industries
Petrochemical industry
food industry
Advantage
- Batch reactors typically have lower initial investment costs compared to CSTR.
- Various number of product making in batch reactor.
- Batch reactor easy to clean.
DisadvantageÂ
- Batch size is limited.
- Batch processes often require more labor and supervision compared to continuous processes.
- Batch processes may result in variations in product quality between batches.
- Maintaining consistent process conditions and product quality in batch reactors can be more complex compared to continuous reactors.
CSTR ( continuous stirred tank reactor)Â
- CSTRs are designed to ensure uniform mixing of reactants throughout the reactor volume.
- This is typically achieved by stirring the contents of the tank using an impeller or agitator.
- Reactant in instantaneously and uniformly mixed throughout the reactor upon entry.
- Output completion is same to composition inside the reactor that is function of residence time and reaction.
- The residence time of reactants in a CSTR can be controlled by adjusting the flow rate of feed materials into the reactor and the volume of the reactor itself.
- CSTRs are equipped with mechanisms for controlling and managing reaction temperatures. This may involve the use of cooling or heating systems, such as jacketed reactors or internal coils, to maintain the desired temperature range for the reaction.
- The C.S.T.R is steady sate equipment. It means the extent of conversion does not depend on the time. The agitator makes the concentration uniform throughout the reactor. It means the extent of conversion does not depend on the location also. The extent of conversion depends on the volume of the reactor.
Advantage
- Temperature control is easily maintained.
- Less expensive and easier to construct than dedicated specialty flow systems.
- CSTRs are designed to achieve thorough mixing of reactants throughout the reactor volume. This ensures that reaction conditions, such as temperature and concentration, are uniform, leading to improved reaction kinetics and higher conversion rates.
- The residence time of reactants in a CSTR can be precisely controlled by adjusting the flow rates of reactants and products. This enables optimization of reaction kinetics, allowing for higher product yields and more efficient use of resources.
- CSTRs can be equipped with efficient cooling or heating systems to control reaction temperatures.
- CSTRs can be easily scaled up or down to accommodate different production volumes.
- Low labour cost.
- Easy way to clean
Disadvantage
- conversion per unit volume of reactor is low.
- not recommended for high pressure operation because of cost consideration.
- not suit for reaction with very high temperature.
- CSTR may suffer from limitations in heat and mass transfer, especially in reactions involving highly viscous fluids or solid-liquid reactions. Inefficient heat and mass transfer can result in non-uniform reaction conditions and reduced overall reaction rates.
Expand Your Knowledge on [Centrifugal pump]
Plug flow reactor
- Many name of plug flow reactor example unmix flow reactor, tubular reactor, piston flow reactor, sludge flow reactor.
- Also known as continuous tubular reactor.
- It is consist of single continuous long tube or several tubes arranged in parallel.
- There are reactants chemical enter at one and product mixture leaves from the other end of reactor.
- Mixing takes place in radial direction only.
- Each plug is considered as separate identify.
- Residence time of plug is a function of its position in reactor.
- Preferred in gas and liquid phase systems.
- Concentration varies along length in case of PFR.
Advantage
- Easy to maintain.
- Highest conversion per unit volume of reactor.
Disadvantage
- Difficult to control temperature with in the reactor.
- hotspot can occur with the exothermic reaction.
Various MOC ( Material of construction ) types Reactor
- SS ( Stainless steel )
- CS ( Cast iron )
- MS ( Mild steel )
- Hastelloy ( Nickel, Molybdenum, Tungsten, Chromium alloy excellent corrosion resistance in wide range of severe environment )
- Inconel Nickel, iron and chromium alloy typically used for acid resistant at high temperature applications, this material forms a thick oxide layer when heated to protect the surface from chemical attack.
- Monel : Nickel and copper alloy with 2:1 ration is probably after SS most commonly used in plant. it has good resistance to diluter acids and has good mechanical properties at higher temperature also.
- Glass lined reactor basically used for storing highly acidic chemical.
Expand Your Knowledge on [Reactor jackets and types]