Glass Lined Reactor
Introduction
In the chemical and pharmaceutical sector, a glass lined reactor is used given their compatibility with a wide range of chemicals. The reactor is a vessel with an agitator that allow the mixing of chemical in contained environment. The reactor can be pressurized and operate in a range of temperatures.
Reactors are used in industries to perform reactions used in the manufacturing process. There are different types of reactors used in chemical industries and we have discussed in a post various type of reactor.
What Is Glass Lined Reactor ?
Glass lined reactor is an outstanding anti-corrosion chemical reaction vessel. It is engineered from different steel lined with a layer of vitreous enamel with high density silicon dioxide.
Different Type Of MOC
MSGL ( Milled Steel Glass Lined)
SSGL ( Stainless Steel Glass Lined)
Glass Lined Reactor Parts
- Dip Pipe & J- Pipe : Dip pipe use for solvent charging
- Mechanical Seal
- Baffles
- Flush bottom valve
- Main hole ( Manways)
- Sight glass (show glass)
- Reactor Jacket
- RTD sensor point ( thermowell point)
- Vapor column nozzle
- Jacket nozzle inlet / outlet
- Agitator and impeller
- Pressure safety valve and Rupture disc
- Steam trap and bypass valve
Expand Your Knowledge on [Rupture Disc]
Glass lined Reactor Agitator types
- Anchor
- Paddle
- Turbine
- Curve
- Propeller
- Gate
- Flame
- Spiral
Glass Lined Reactor Use
The primary use is chemical mixing and variants are the pressure, temperature, gases used and catalyst. Glass lined reactor to be cleaned to a high standard which prevent batch carry over.
Chemical processing
Glass-lined equipment is widely used in the chemical processing industry, where it is used to handle corrosive chemicals, acids, and alkalis. Glass-lined vessels, reactors, and pipes are commonly used in chemical processing plants.
Pharmaceutical manufacturing
Glass-lined equipment is also commonly used in pharmaceutical manufacturing, where it is used to handle sensitive materials and prevent contamination. Glass-lined reactors and vessels are often used in the production of drugs and other pharmaceutical products.
Food and beverage processing
Glass-lined equipment is used in the food and beverage industry to ensure product purity and prevent contamination. Glass-lined vessels, tanks, and pipes are used to store, process, and transport food and beverage products.
Water treatment
Glass-lined equipment is used in the water treatment industry to handle the harsh chemicals and materials used in water treatment processes. Glass-lined tanks and pipes are used in water treatment plants to store, process, and transport water.
Petrochemical processing
Glass-lined equipment is used in the petrochemical industry to handle harsh chemicals, acids, and solvents. Glass-lined vessels, reactors, and pipes are commonly used in petrochemical processing plants.
Expand Your Knowledge on [Reactor Jackets types, benefits and uses]
Glass lined Reactor Selection Criteria
Here are some of the points that we need to consider prior to selecting the MOC of the rector.
Process safety
Prior to selecting the reactor, it is essential to check whether the selected reactor is safe for the process. There should be no hazard associated with the selection of the MOC of the reactor.
Operating pressure and temperature
Every MOC has an operating range of parameters such as temperature and pressure. It is to be checked if the selection of reactor is under an operating range of pressure and temperature.
Chemical Compatibility
Incompatible chemicals can severely damage the reactor MOC and also cause safety issues. It is recommended to check whether the chemical which is going to be used in the reactors are compatible with each other or not.
Cost
Cost is another factor that we need to take into consideration. The Selected MOC of the reactor should be cost-effective.
As we discussed above, these are the points that we need to take into consideration while selecting reactors.
We had discussed chemical compatibility above in short, let us discuss this point in detail. Selection of reactor of which type of MOC of the reactor is to be selected depends on the reaction mass ph. There are different types of MOC of reactors are available and among those, reactors can be broadly classified as stainless-steel reactors (SS) and other is Glass lined reactors.
If the reaction mass media is basic or after dosing of chemical and raw materials, it will remain basic then stainless steel reactors will be suitable for the reaction process. Acidic media can oxidize the MOC and can corrode the stainless steel reactor to some extend, hence for the protection of the reactor, only basic and neutral media of reaction mass is used in stainless steel reactor. If the reaction mass is acidic or after the addition of chemicals the pH will become acidic, then Glass lined reactors are preferred.
Glass Lining & Applications
Properties of glass
Glass is lined in reactor with borosilicate 3.3
80% Silica
13% Boron oxide
4% Sodium oxide
2-3% Aluminum oxide
Boron oxide thermal expansion is very low 5-7 (µ).
Borosilicate glass 3.3 is very low weight. (atomic weight 10.81 g/mol)
Trade name of glass in lining is known simax, suprax, pyrex, endral, refmax.
Glass lining colour
01. Blue
02. Light blue
03. White
04. Green
01. Blue Lining
- Higher thermal conductivity
- Blue Lining Reactor is used high concentrated acid
- It provide maximum protection against concentrated acid.
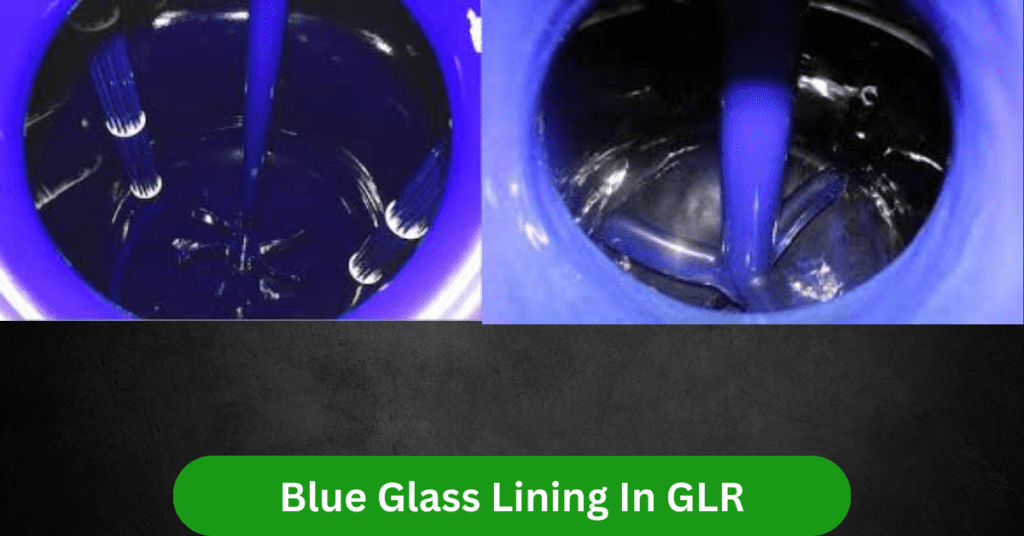
02. Light Blue Lining
- Light blue glass lining reactor used in pharma industry.
- This colour is better visual optical monitoring.
- Corrosive resistance is low to dark blue colour.
- Cross check to clean properly.
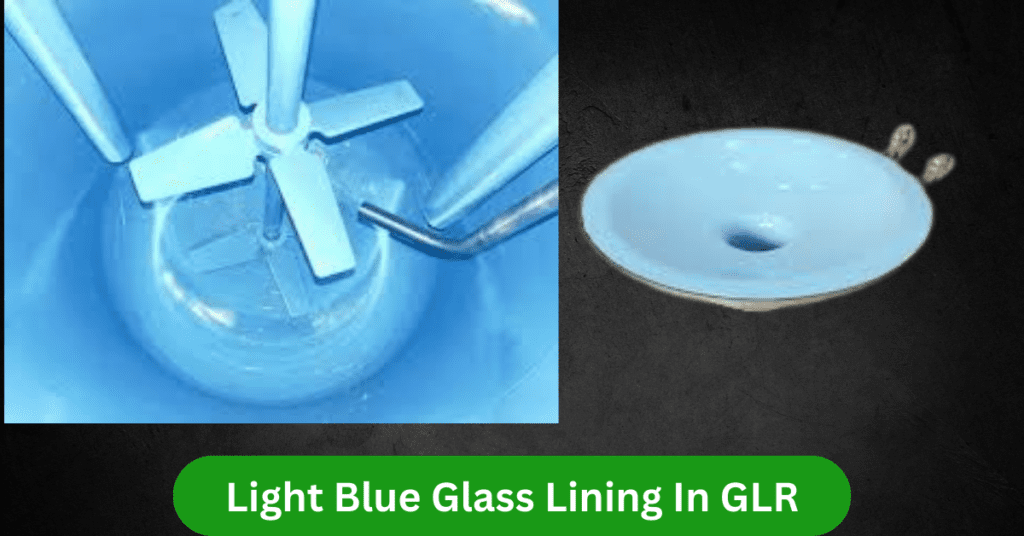
03. Green Lining
- Green glass use to handle reaction carried at high temperature.
- Maximum temperature handle in glass lined reactor 270 degree C.
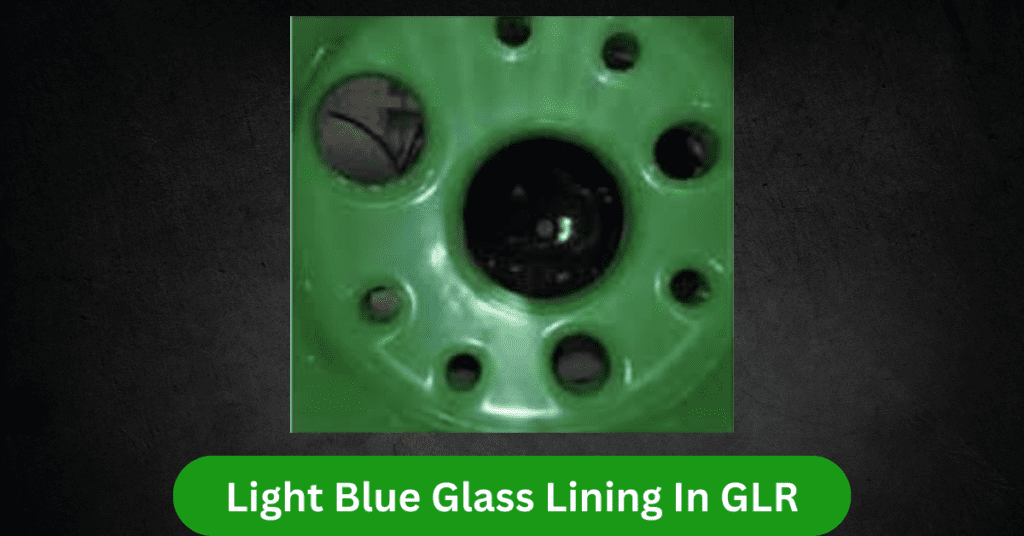
04. White Lining
- White glass lining is used for that types of processes in which colors changing in process.
- Easy Observation in colorful Reaction ( Like Photo chemical )
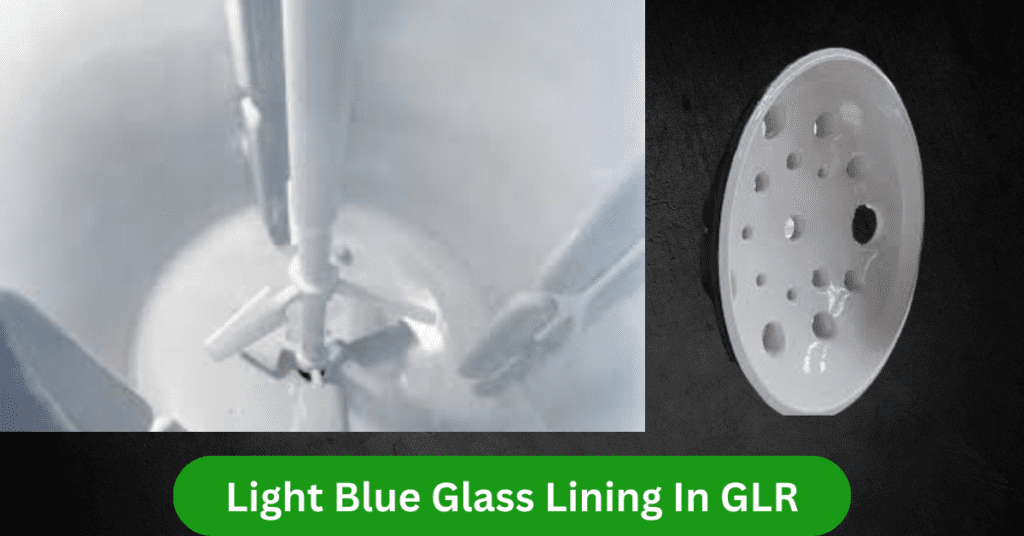
Glass Lined Reactor Thickness
- Glass lining thickness 1mm -2.2mm
Spark Test Glass Lined Reactor
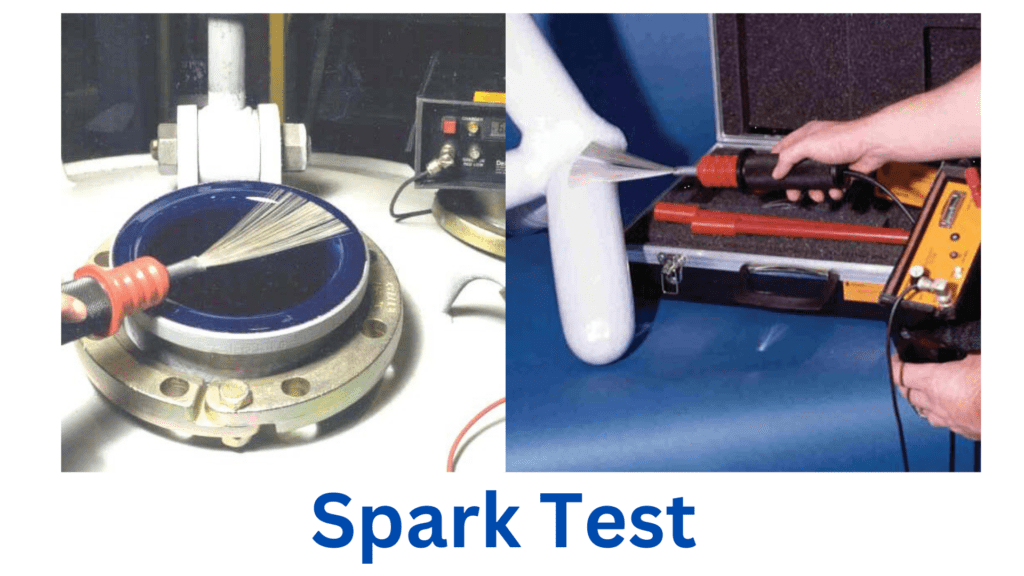
A glass-lined reactor or glass-lined equipment has a lining of glass which over time of use can be damaged.
There are multiple factors responsible for the damage of glass lining for glass chipping, cracks, pinholes, or peeled off.
Glass lining is tested electrically through a spark test is a test that is used to detect the defect or damaged part of glass lining and help to mark those locations.
In spark test, there are two types of apparatus:
- 5KV AC Apparatus
- 5KV DC Apparatus
In spark test, AC or DC apparatus is connected with a broom. The surface of the reactor which has a glass lining is brushed using a broom. If a defect or damaged part comes in contact with the broom, it generates a spark as the damaged part exposes MS or CS material.
As the spark is generated, we can mark those locations as damaged parts. In this way, damages, defects, or peeled-off places of glass lining are detected.
Reactors are used in industries to perform reactions used in the manufacturing process. There are different types of reactors used in chemical industries and we have discussed in a post various types of reactor.
Expand Your Knowledge on [Equivalent Weight]
How to Repair small damages of GLR
- The damage of GLR surface, no matter how to small must be repair immediately to prevent corrosion of base metal and avoid further damage to the lining.
- In case of pin hole or damage of glass smaller than 8mm dia.
- use plug with PTFE washer with Tantalum plug.
How to prevent thermal shock in GLR
- Preventing thermal shock in a glass-lined reactor is crucial to maintaining the integrity of the reactor vessel and preventing damage or failure. Thermal shock occurs when there is a rapid and uneven change in temperature within the reactor, causing stress on the glass lining.
- Avoid sudden changes in temperature within the reactor. When heating or cooling the reactor, do so gradually to allow the glass lining to expand or contract uniformly, reducing thermal stress.
Q&A
- What is a glass reactor ?
ANS. Glass lined reactor is an outstanding anti-corrosion chemical reaction vessel. It is engineered from different steel lined with a layer of vitreous enamel with high density silicon dioxide.
2. What is the thickness of GLR ?
ANS. Glass lining thickness 1mm -2.2mm
3. What is glass-lined material ?
ANS. Glass lined material is a specialized industrial coating that combines the chemical resistance of glass with the mechanical strength of metal.
4. Which glass used in GLR ?
ANS. Glass is lined in reactor with borosilicate 3.3
80% Silica, 13% Boron oxide, 4% Sodium oxide, 2-3% Aluminum oxide
5. Why is glass-lined reactor color blue ?
ANS. The blue color of a glass-lined reactor is due to the cobalt based enamel coating used in the glass-lining process.