Glass Lined Reactor Interview Questions
Introduction about glass lined reactor interview questions :
Glass-lined reactors are the most important commodities in the pharmaceutical, chemical, and food processing industries, owing to excellent corrosion resistance and superior compatibility with chemicals, besides durability. Questions pertaining to glass-lined reactors are commonly inquired in most aspects, mainly concerning construction, maintenance, safety factors, and process-related considerations. The present note would suffice as a collection of frequently asked questions and answers in relation to their preparation for interviews by professionals. It covers a vast scope of topics from technical specifications and safety measures to troubleshooting and regulatory standards.
01. What is a glass-lined reactor ?
Ans. A glass-lined reactor is a type of chemical reactor that features a glass coating on its inner surface.
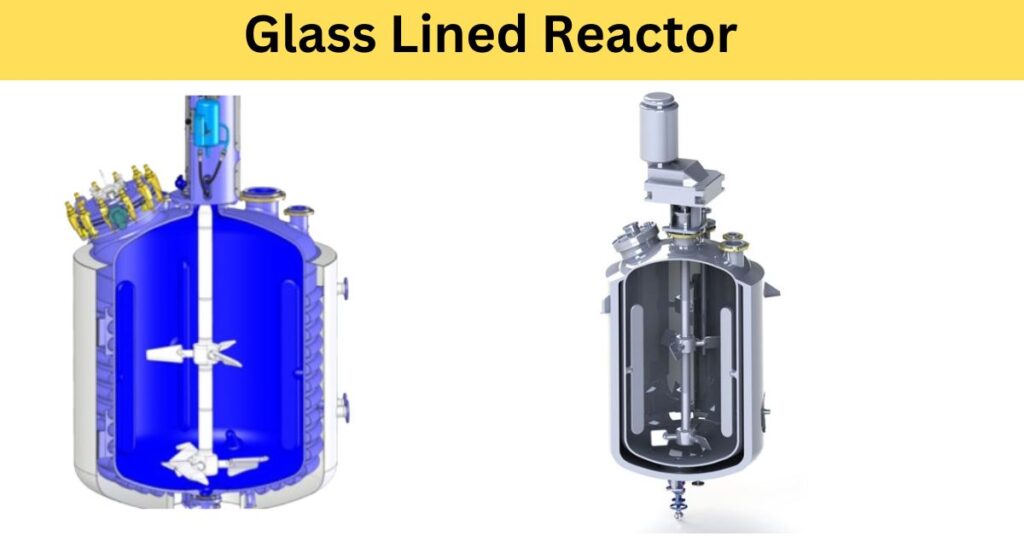
02. What are the main advantages of using glass-lined reactors ?
Ans. Prevents contamination of products. Reduces maintenance costs due to its corrosion resistance. Suitable for multi-purpose applications due to its wide range of chemical compatibility.
03. Describe the construction of a glass-lined reactor.Â
Ans. Main Body : The main part of the reactor is made of strong carbon steel, which provides support and strength.
Glass Lining : The inside surface is coated with a special glass layer. This glass is baked onto the steel at high temperatures in several steps to make it durable and resistant to chemicals.
Nozzles and Manway : On the top of the reactor, there are nozzles for connecting pipes and other equipment, as well as a manway, which is a small opening for access or inspection.
Baffles : Baffles are plates or structures inside the reactor that improve mixing by reducing swirling of liquids.
Dip Pipes : Dip pipes are tubes used for adding or removing liquids and gases inside the reactor.
Agitator : The reactor has an agitator, a mixing device that stirs the contents. It includes a mechanical seal to prevent leaks.
Tank Outlet Valve : At the bottom of the reactor, there is a valve for removing the final product or waste.
Jacket : Around the reactor, there is a jacket (a second layer) for heating or cooling the contents by circulating water, steam, or oil. Bursting Discs and Sight
Glasses :Â Bursting discs protect the reactor by releasing pressure if it becomes too high. Sight glasses allow operators to look inside and monitor the process.
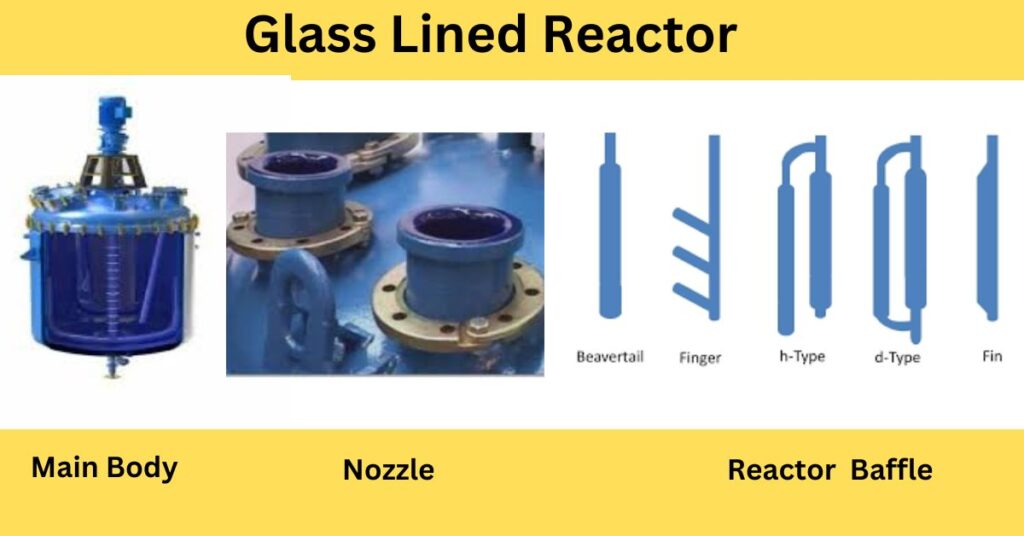
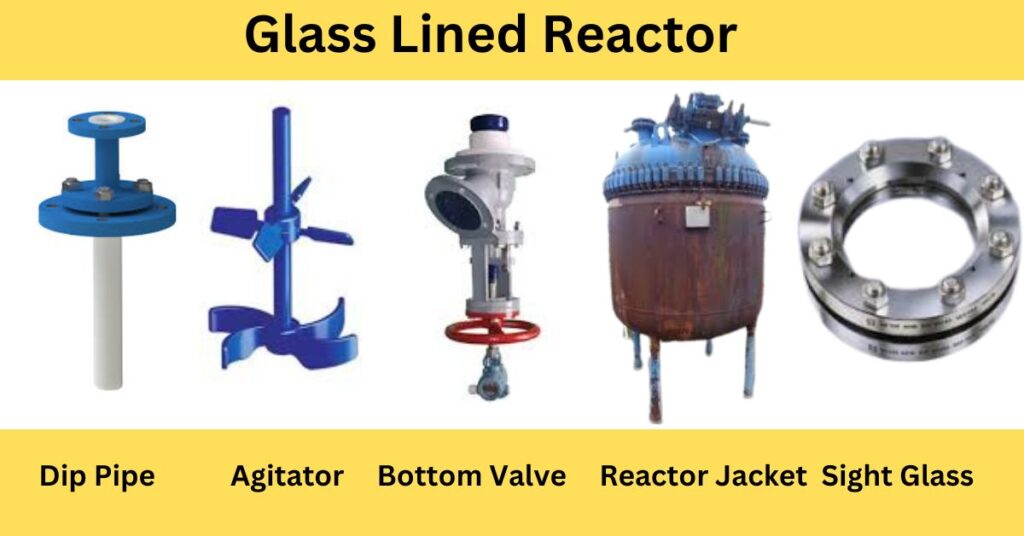
04. What is the purpose of the glass lining in these reactors ?
Ans.
Corrosion Resistance : The glass lining does not get damaged by strong chemicals like acids, alkalis, or water. This makes it perfect for tough environments where other materials would rust or wear out.
Easy to Clean : The glass surface is smooth and non-sticky, so materials don’t stick to it. This makes cleaning simple and keeps the product pure.
Handles Sudden Temperature Changes : Glass-lined reactors can handle quick changes in temperature, which is important for processes that involve heating and cooling.
No Contamination : The glass lining doesn’t react with the materials inside, so it keeps the process clean and prevents any contamination. Smooth Surface : The smooth glass surface helps keep the reactor clean and free of unwanted buildup, ensuring high-quality production.
05. What are the thicknesses of glass lined reactor ?
Ans. The standard thickness of glass lined reactor is between 1 – 2.2 mm, 40-90 mils.
06. How is the thickness of glass lining inspected or measured over time ?
Ans. However, virtually all common glass products can easily be measured with ultrasonic thickness gauge, magnetic thickness gauges, vernier calipers, micrometer. Testing with these glass thickness gauges does not damage the glass, and thickness measurements are instant, accurate, and reliable.
07. What is the maximum temperature limit for a glass lined reactor ?
Ans. The minimum temperature allowance for a standard glass-lined -60 °C.
The maximum temperature allowance for a standard glass-lined +260 °C.
08. What is the pressure range of a glass lined reactor ?
Ans. The pressure ranges are full vacuum (F.V) to +6kg/cm2.
09. Which type of glass is used in a glass-lined reactor ?
Ans. Glass is lined in reactor with
borosilicate 3.3
80% Silica
13% Boron oxide
4% Sodium oxide
2-3% Aluminum oxide
10. Which types of reactions or processes are suited for glass-lined reactors ?
Ans. They are ideal for hydrolyzing, hydrogenation, acidification, neutralizing, crystallizing, mixing, emulsifying and other reactions.
11. How does a glass-lined reactor handle exothermic reactions ?
Ans. Glass-lined reactors can handle exothermic reactions by using wall-mounted baffles to improve heat transfer and temperature control.
12. Explain how temperature is controlled within a glass-lined reactor ?
Ans. The temperature in a glass-lined reactor is controlled by circulation a heating and cooling medium through jacket.
13. Which agitator is used in glass lined reactor?
Ans.
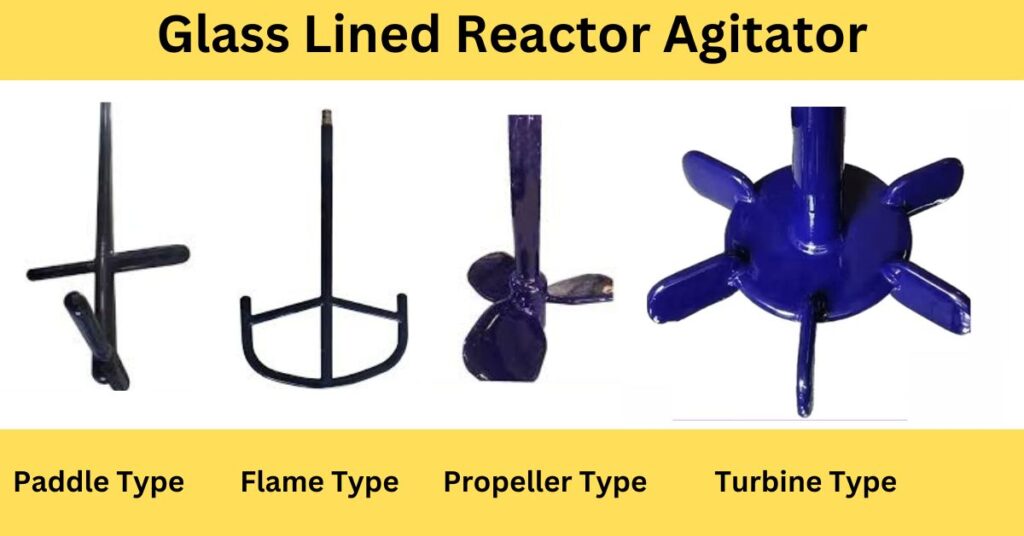
The types of agitator are paddle, flame, propeller, anchor, turbine, helical, screw agitator used in glass-lined reactor.
14. How does agitation affect heat transfer and reaction rate in glass-lined reactors ?
Ans. Ans. Agitation in a glass-lined reactor can affect heat transfer and reaction rate in the following ways:
Heat transfer : Agitation increases heat transfer coefficients because the agitator draws in fresh air and expels hot air. The overall heat-transfer coefficient for an agitated batch in a glass-lined reactor is usually between 5-50 Btu/(h)([ft.sup.2])(degrees]F).
Reaction rate : Agitation can help distribute substances more effectively in the reactor chamber, which can lead to faster reactions.
Energy efficiency : Shorter process times or reduced speeds can save energy.
15. What role does a rupture disc play in glass-lined reactors ?
Ans. The rupture disc designed for protect from damaging over/excess pressure and prevent product loss.
16.What is the pH range for a glass-lined reactor ?
Ans. A glass-lined reactor is used for reactions within neutral and acidic pH ranges, as it provides excellent resistance to corrosion and ensures the purity of the processed materials.
Strong base like a NaOH, KOH use in room temperature and Strong alkalis at high temperatures, as they may attack the glass over time.
17. What are the common causes of glass-lining failure ?
Ans. This most common cause of glass-lining failure is :
Mechanical shock
Thermal shock
Cavitation
Hydro blasting
Acid corrosion
18. What methods are used to detect glass lining damage ?
Ans. Glass lining damage is detected using spark testing, visual inspection, ultrasonic testing, thermal imaging, and dye penetration tests.
19. How do you handle minor cracks or chips in the glass lining ?
Ans. Minor cracks or chips in the glass lining are applying glass glue, tantalum plug/ plate, belzona 1392.
20. What safety precautions should be taken when operating a glass-lined reactor ?
Ans. Wear personal protective equipment(PPE’S), Inspect Before Use, Monitor Conditions, Handle Chemicals Safely, Control Static Electricity, Detect Leaks, Perform Maintenance, Follow SOPs.
21. How can pressure and temperature fluctuations impact the glass lining ?
Ans. Pressure and temperature variations can severely affect on the glass lining :
Thermal Shock : Temperatures increase or decrease rapidly, causing stress to be built up within the glass lining to crack or detach from the lining.
Mechanical Stress : Abrupt changes in pressure create stress on the glass-lined surface, such that micro-cracks can form or the bonding between the glass and the metal can be compromised.
Glass Brittleness : The repeated stress, over time, makes the glass lining brittle; hence, the operation can sometimes damage it. please give this answer in a short step.
22. What PPE is essential for operators working with glass-lined reactors ?
Ans. When working on glass lined reactors, operator should be wear safety helmet, safety googles, safety shoes, hand gloves are as per using handling of chemicals and operations.
23. What steps would you take if the glass lining was accidentally exposed to hydrofluoric acid ?
Ans. Hydrofluoric acid (HF) should not be used in a glass-lined reactor because it reacts with the glass lining (made of silicon dioxide). The fluorine in HF breaks the bond between silicon and oxygen, dissolving the glass, which can damage the reactor and lead to operational hazard.
24.If you find a leak in the reactor, what immediate actions should you take ?
Ans.
Shut down procedure : Halt reactor operation and close valves, which isolates the reactor from other systems, so that nothing more than chemical release or pressure build-up happens. Let people be evacuated to a safe place if chemicals are hazardous; initiate emergency response and contact the officer or teams.
Assess the Leak : Find what the leak source is and monitor the pressure gauge to know how much leak has happened and probable damage.
Control the Leak : If it is safe not to cause a hazard, control leaks with absorbents and/or spill containment kits, sealing the leak temporarily in place with suitable sealing methods.
Call Maintenance : Contact maintenance or engineering immediately for on-site assessment and repair, and maintain the company procedure for documentation.
Check for Damage : Cool down the reactor first, then check the glass lining of the reactor for cracks or imperfections. Use some form of non-destructive testing, such as a spark test, to identify further damage.
Repair the Leak : In more severe cases, re-glass the reactor or repair broken areas using the correct repair compound. Test for leaks after all repairs have been completed to ensure a good seal.
Check for Hazards : It should be ascertained that no environmental contamination has occurred and that all the various safety systems such as alarms, pressure relief valves etc are functioning.
Restart Operation : After the repairs as well as safety checks are performed, the reactor can be slowly brought up while continuously monitoring for other problems which could be surfacing.
25. What regulatory standards apply to glass-lined reactors in chemical processing ?
Ans.
DIN 28721 : This standard specifies the quality requirements for vitreous enamel used in glass-lined equipment. It covers aspects like glass thickness, visual quality, and the overall glazing quality of the lining.
ASME Boiler & Pressure Vessel Code : This standard ensures that glass-lined equipment meets safety and durability expectations. Glass-lined equipment is categorized under ASME Section VIII, Div. 1, which addresses design, construction, and operation of pressure vessels.
Other Global Pressure Vessel Regulations :
- AD 2000 : A set of rules for pressure vessels, mainly used in Europe, covering design, fabrication, and testing.
- PED (Pressure Equipment Directive) : A European Union standard ensuring safety and performance for pressure equipment.
- TEMA (Tubular Exchanger Manufacturers Association) : Covers standards for heat exchangers, including those made of glass-lined material.
- GHOST, SELO : Certifications and standards that ensure the safety and quality of pressure vessels.
- GB150 : A Chinese standard for the design and construction of pressure vessels.
- KGS : Standards from Korea for pressure vessels, ensuring safety and quality.
26. Explain the importance of leak tests in glass-lined reactor maintenance.
Ans. Leak tests are critical in maintaining the safety, efficiency, and longevity of glass-lined reactors.
Methods for Leak Testing :
Pressure testing : The reactor is pressurized with air or water to check for leaks.
Vacuum testing : A vacuum is applied to detect leaks in the reactor’s lining.
Dye testing : A special dye is applied to the reactor, and leaks are detected based on the presence of the dye.
Spark testing : High-voltage electrical current is applied to detect any breach in the glass lining.
27. What is a glass-lined reactor spark test ?
Ans. A spark test is used to detect defects or cracks in a glass-lined reactor. When a high-voltage electric current is applied, sparks are obtained if any defects exist in the lining.
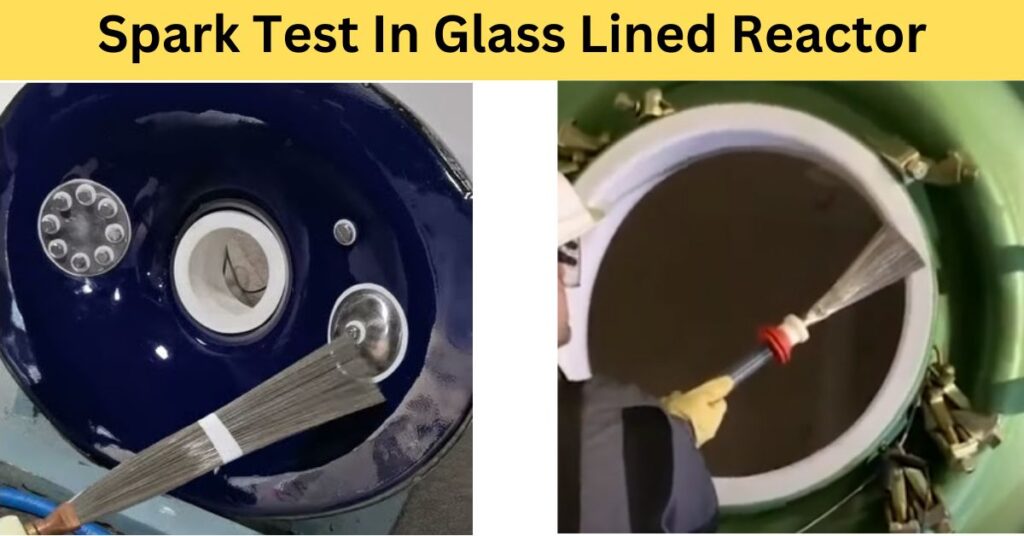
28. What voltage is typically used during a spark test on a glass-lined reactor ?
Ans. The voltage used in a spark test for a glass-lined reactor typically ranges from 6 kV to 30 kV. The exact voltage depends on the reactor’s size and the thickness of the glass lining.
29. What is the process of performing a spark test on a glass-lined reactor ?
Ans. An electrode is used, together with a probe moved across the reactor’s glass surface. Sparks will indicate cracks or defects.
30. Why is the spark test of importance to glass-lined reactors ?
Ans. This is because the test helps detect some hidden damage within the glass lining that could cause some rusting of the metal beneath. It ensures that the reactor remains safe and effective in preventing leaks or failures.
31. What if a spark test indicates damage in the glass lining ?
Ans. When damage is indicated, the damaged area is scored so that the area can be repaired. The severity may require only the application of a glass repair compound while, in worse cases, one has to re-glass the reactor.
32. How frequently should a glass-lined reactor undergo a spark test ?
Ans. A spark test should be carried out periodically, say annually, or after repairs, following any considerable alterations in its operation, or a change in temperature. Regular testing helps keep the reactor in good order.
33. Are glass-lined reactors available in different colors ?
Ans. Glass-lined reactors are typically available in blue, but they can also come in other colors such as white or light blue, green depending on specific requirements and applications. The color is mainly for visual identification and does not impact the reactor’s performance.
34. How are the level measurement marks made on agitators ?
Ans. Level measurement marks on agitators are made by adding contrasting glass colors during the manufacturing process. These marks provide a clear visual indication for level measurement.
Examples :
White Agitator with Blue Marks : Blue lines are fused on to a white glass agitator for visibility.
Blue Agitator with White Marks : White lines are added to a blue glass agitator for contrast.
35. Why is glass-lined reactor color blue ?
Ans. Glass-lined reactors are blue because cobalt oxide is added during the glass manufacturing process. This imparts the characteristic blue color to the glass lining.
36. What is the pH range for a glass-lined reactor ?
Ans. Glass-lined reactors are ideal for acidic and neutral reactions. They can also handle alkali reactions, but only at low temperatures, typically below 30°C, to prevent damage to the glass lining from alkali attack.
37. Why is caustic not used at high temperature in a glass-lined reactor ?
Ans. Hot caustic alkalis like sodium hydroxide and potassium hydroxide react with glass, dissolving its silica content and forming sodium silicate. This reaction weakens the glass lining, leading to equipment damage and reduced service life, making alkalis hazardous for glass-lined reactors.
38. What is glass lining ?
Ans. Glass lining is a process where a glass coating is applied to the inside of equipment to protect it from corrosion and contamination. This is done by coating the equipment with glass powder and heating it in a furnace to bond the glass to the metal surface.
39. Why is the tantalum plug used in a glass-lined reactor ?
Ans. A tantalum plug is used in a glass-lined reactor for its exceptional corrosion resistance. Tantalum is highly resistant to most acids, including hydrochloric and sulfuric acids, even at high temperatures.
40. Where is earthing provided in glass line reactor ?
Ans. Earthing in a glass-lined reactor is essential for the thermowell and bottom outlet valve with a tantalum plug to safely dissipate static electricity and prevent sparking.
Conclusion
Understanding of complexities in glass-lined reactors is highly important for working professionals in businesses applying these niche reactors. This all-inclusive interview guide preps well-rounded answers on such construction operations, maintenance, and safety issues. Hence, learning these areas will not only help the candidate improve their responses to their interviewers but will also enhance professional expertise in handling glass-lined reactors – thereby making industrial processes safer and more efficient.